Optimize Your Production with Advanced Blow Molding Machines for Efficient Manufacturing
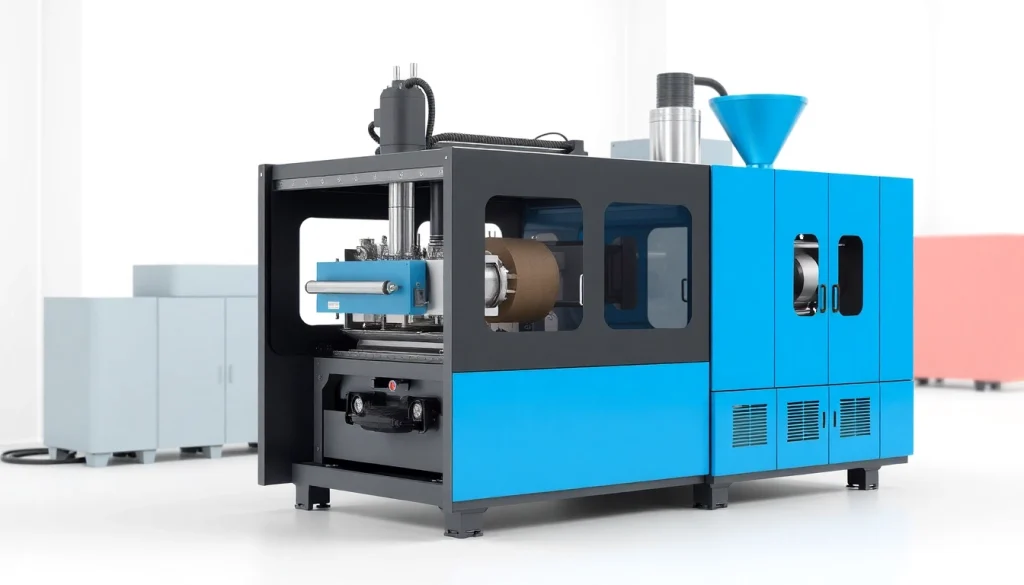
Introduction to Blow Molding Machines
In today’s manufacturing landscape, the demand for lightweight and durable plastic products has significantly increased. Central to meeting this demand are blow molding machines, which are essential in producing hollow plastic parts efficiently. This process is widely used in various industries, from packaging to automotive components. Understanding the functionality, benefits, and applications of these machines is crucial for manufacturers aiming to optimize their production line.
What is a Blow Molding Machine?
A blow molding machine is a piece of industrial equipment used to create hollow plastic parts by blowing air into a heated thermoplastic material. The basic concept involves heating plastic until it becomes pliable, shaping it into a parison (a tube-like structure), and then inflating it into a mold to produce the desired shape. This fundamental process can be adapted for various production scales, from small operations to large-scale manufacturing lines.
History and Evolution of Blow Molding
The blow molding technique dates back to the early 20th century, with significant advancements made over the decades. Initially, the process was performed manually, with artisans shaping and blowing into molten glass. With the advent of plastic materials after World War II, the blow molding industry began to evolve rapidly, embracing modern technology and automation. Today, blow molding machines incorporate advanced features such as computer control systems, improving precision, efficiency, and speed, thus revolutionizing how mass-produced plastic items are created.
Benefits of Using Blow Molding Technology
Blow molding technology presents numerous advantages:
- Cost-Effectiveness: The energy costs involved in producing large volumes are significantly lower compared to other manufacturing methods.
- Speed: With automated systems, blow molding machines can achieve high production rates – often manufacturing thousands of units per hour.
- Versatility: This technology accommodates a variety of plastic types and can produce shapes ranging from simple to complex geometries.
- Lightweight Products: The hollow structure of blown products reduces weight without sacrificing strength, a desirable quality in many applications.
Types of Blow Molding Machines
There are several key types of blow molding machines, each suited for specific applications and materials. Understanding these types helps manufacturers select the right equipment for their production needs.
Extrusion Blow Molding Machines
Extrusion blow molding (EBM) machines are designed to create containers by extruding molten plastic into a tube and then blowing it into a mold. This method is typically used for producing items such as bottles, tanks, and industrial containers. EBM is known for its high efficiency and lower costs, as it allows for the quick production of large batches. Notably, it also enables the creation of complex shapes while minimizing material waste.
Injection Blow Molding Machines
Injection blow molding (IBM) combines the processes of injection and blow molding to produce high-quality, precise parts. In this method, a plastic preform is injected into a mold, then transferred to a blowing station where air is introduced to create the final shape. IBM is ideal for producing small bottles and containers with high dimensional accuracy, making it suitable for the pharmaceutical and cosmetic industries.
Stretch Blow Molding Machines
Stretch blow molding (SBM) utilizes a two-step process involving the creation of a preform followed by stretching and inflation in the mold. This technique is particularly effective for producing PET bottles and has become increasingly popular due to its ability to create stronger, lighter bottles with great clarity. SBM achieves superior results, ranging from enhanced mechanical properties to improved barrier performance, catering specifically to the beverage market.
Key Features to Consider When Buying a Blow Molding Machine
Investing in a blow molding machine is a significant decision for any manufacturer. Here are critical features to consider:
Production Capacity and Speed
One of the first features to evaluate is the machine’s production capacity and speed. Understanding your production requirements will help you choose a machine capable of meeting your output goals. Look for machines that offer flexibility in production rates, as demand may fluctuate over time.
Energy Efficiency Standards
Energy efficiency is a major factor in operational costs, especially in large manufacturing settings. Machines that comply with the latest energy efficiency standards can significantly reduce long-term expenses while also minimizing the environmental impact of production processes. Consider models that incorporate energy-saving technologies like servo pumps and variable frequency drives.
Automation and Control Features
Modern blow molding machines come equipped with various automation features to enhance operational efficiency. Look for models with programmable logic controllers (PLCs), touch screen interfaces, and remote monitoring capabilities. These features can streamline workflows and allow for easier adjustments, ensuring consistent product quality.
Applications of Blow Molding Machines
Blow molding machines are versatile and used across multiple industries. Here are some common applications:
Beverage Bottles and Containers
The most recognized application of blow molding is in the beverage industry, particularly for creating plastic bottles. This application encompasses everything from soft drink bottles to water containers. The technology allows for the efficient production of lightweight and recyclable bottles, contributing to both cost-effectiveness and sustainability in packaging.
Industrial Applications
Beyond consumer products, blow molding is utilized in producing large-scale industrial components such as tanks, bins, and specialized containers that require durability and specific functionalities. These components are often made from high-density polyethylene (HDPE) or similar materials to withstand harsh working conditions.
Packaging Solutions for Consumer Goods
Various consumer goods require unique packaging solutions that blow molding can effectively provide. This includes packaging for household goods, cosmetics, and pharmaceuticals. The customizability of mold designs allows manufacturers to create packaging that not only serves its purpose but also enhances brand appeal.
Future Trends in Blow Molding Machine Technology
The field of blow molding technology is constantly evolving. Here are some trends shaping its future:
Smart Technologies and IoT Integration
As smart technologies make their way into manufacturing, blow molding machines are also being equipped with IoT features for enhanced monitoring and control. Predictive maintenance systems can reduce downtime, while data analytics help improve efficiency by identifying bottlenecks and guiding operators to optimize processes. The integration of AI can lead to self-adjusting parameters that enhance production quality.
Sustainable Practices in Blow Molding
With increasing environmental awareness, the blow molding industry is moving toward sustainable practices. This includes using recycled materials and designing products that are easier to recycle. Furthermore, innovations in bioplastics are being explored, providing eco-friendly alternatives without sacrificing performance.
Market Growth and Innovations
The global blow molding machine market is expected to grow significantly over the next few years, driven by rising demand across multiple sectors. New advancements in machine design and the ongoing development of multi-layer and injection blow molding technologies are pushing the boundaries of traditional manufacturing. This evolution will allow the industry to meet specific consumer demands while also addressing sustainability concerns.