Leading-Edge Blow Molding Machine Solutions for Efficient Production
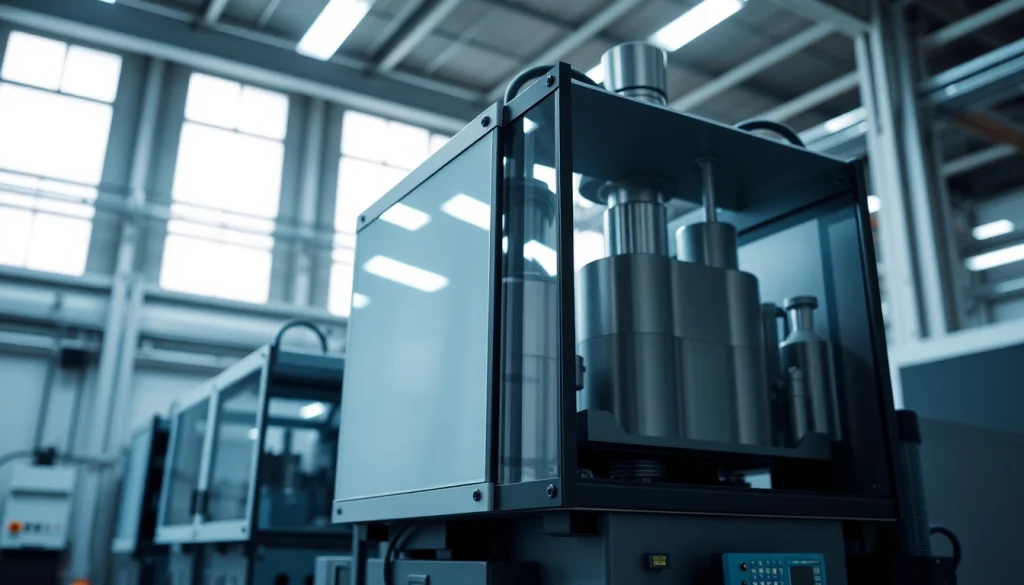
1. Understanding Blow Molding Machines
1.1 What is a Blow Molding Machine?
A blow molding machine is a sophisticated piece of manufacturing equipment used to create hollow plastic products. The machine operates through a process that involves heating, shaping, and cooling plastics into desired forms, usually in the production of containers, bottles, and various industrial components. The method of manufacturing employs a high degree of precision and can be customized for mass production, thus becoming an invaluable asset in industries ranging from packaging to automotive engineering.
In essence, a blow molding machine works by forming a plastic parison — a hollow tube — which is then inflated against the inner walls of a mold. As air pressure blows the parison into the shape of the mold, the material cools and solidifies, resulting in a finished plastic product. For a detailed overview of specific machine functionalities, consider examining this Blow Molding Machine.
1.2 Applications of Blow Molding Machines
Blow molding machines are utilized in numerous applications due to their versatility and efficiency. Here are several common uses:
- Packaging: The most prevalent application includes the production of plastic bottles for beverages, sauces, and household chemicals.
- Automotive Parts: Production of fuel tanks, bumpers, and various inner parts.
- Household Products: Items such as storage containers, large jugs, and toys can be manufactured.
- Industrial Applications: Used in creating large, complex shapes for various industries.
1.3 Advantages of Using Blow Molding Technology
Adopting blow molding technology presents several advantages:
- Cost Efficiency: Ideal for mass production, reducing the cost per unit significantly.
- Flexibility: Capable of producing a wide range of product sizes and shapes.
- Material Efficiency: Minimizes waste with precise material usage and can incorporate recycled materials.
- Durability: Creates strong, lightweight products that can withstand various conditions.
2. Types of Blow Molding Machines
2.1 Extrusion Blow Molding
Extrusion blow molding (EBM) is the most common type of blow molding technique used to create hollow plastic parts. The process begins by melting raw plastic resin and extruding it into the shape of a parison. Here is a breakdown of the EBM process:
- The plastic resin is heated until it melts.
- The melted plastic is formed into a parison.
- The parison is clamped into a mold, and air is blown into it to shape it according to the mold design.
- The formed item is cooled and removed from the mold.
The extrusion blow molding process is particularly suited for manufacturing a variety of containers, including bottles and jugs, due to its flexibility and efficiency.
2.2 Injection Blow Molding
Injection blow molding (IBM) is a method that combines injection molding and blow molding to produce precise, complex shapes. This process is defined as follows:
- The process begins with injection molding, where the plastic is injected into a preform mold and cooled.
- The cooled preform is then transferred to a blow mold.
- Compressed air is blown into the preform to shape it into the final product.
This technique is often favored for products requiring high dimensional accuracy, and it is commonly used in producing smaller and more intricate items, such as pharmaceutical bottles.
2.3 Stretch Blow Molding
Stretch blow molding (SBM) is an advanced method that stretches the parison both axially and radially before inflating it in the mold. The key benefits of this process include:
- Enhanced Strength: Products exhibit superior strength and barrier properties.
- Clarity: The process allows for improved clarity and aesthetics in the final product.
This type is primarily used for producing high-quality PET bottles for beverages, where the integrity of the container is crucial for maintaining freshness.
3. Key Features to Consider When Selecting a Blow Molding Machine
3.1 Capacity and Production Speed
When selecting a blow molding machine, one of the primary factors to consider is the production capacity and speed. Depending on the industry requirements, machines can vary significantly. Key considerations include:
- Output Volume: Evaluate the number of units produced per hour, as this directly affects manufacturing competitiveness.
- Cycle Time: The time it takes to complete one cycle (from forming the parison to finished product) is crucial for time-sensitive production.
3.2 Energy Efficiency and Costs
Energy efficiency is becoming a critical aspect of machine selection due to rising energy costs and environmental regulations. Therefore, consider the following:
- Energy Consumption: Investigate the machine’s energy efficiency ratings and potential cost savings over time.
- Operating Costs: Include operational and maintenance costs in your calculations to accurately evaluate long-term investments.
3.3 Automation and User-Friendliness
Effective automation increases productivity and reduces labor costs. Key features to look out for include:
- Control Systems: Modern blow molding machines often feature advanced control systems that allow for easy operation and programming.
- Maintenance Features: Machines designed with accessibility for maintenance ensure longevity and reduce downtime.
4. Innovations in Blow Molding Technology
4.1 Integration of Smart Technologies
Advancements in smart manufacturing technologies are profoundly impacting the blow molding industry. Key innovations include:
- IoT Integration: Internet of Things (IoT) technology allows real-time monitoring and data analytics of machine performance.
- Predictive Maintenance: Smart sensors can detect potential issues before they lead to machine failure, optimizing maintenance schedules and minimizing downtime.
4.2 Sustainability in Blow Molding
Sustainability has become a focal point for industries. Recent innovations are addressing this by:
- Recyclable Materials: Many manufacturers are now able to utilize recycled plastics as raw material, significantly reducing waste.
- Energy-efficient Machines: New machines are designed to consume less electricity while maximizing output, contributing to lower carbon footprints.
4.3 The Future of Blow Molding Machines
As technology continues to evolve, the future for blow molding machines looks promising. Trends indicate:
- Increased Customization: The ability to create custom molds with shorter lead times will enhance production flexibility.
- Advanced Materials: Research into alternative materials can lead to more eco-friendly products while maintaining performance standards.
5. Frequently Asked Questions about Blow Molding Machines
5.1 How Does a Blow Molding Machine Work?
A blow molding machine operates by heating and shaping plastic materials into hollow forms. Initially, plastic resin is melted and formed into a parison which is then inflated within a mold using compressed air.
5.2 Cost Analysis for Blow Molding Machines
The cost of blow molding machines can vary widely based on their complexity, type, and features. A budget should be made considering initial costs as well as long-term operational expenses.
5.3 Common Mistakes to Avoid when Operating Blow Molding Machines
When operating blow molding machines, common pitfalls include:
- Failure to maintain consistent raw material quality.
- Neglecting scheduled maintenance operations, leading to increased machine downtime.
- Not training operators adequately on machine functions and best practices.