Essential Insights and Best Practices for Hydrogen Cyanide Monitor Usage
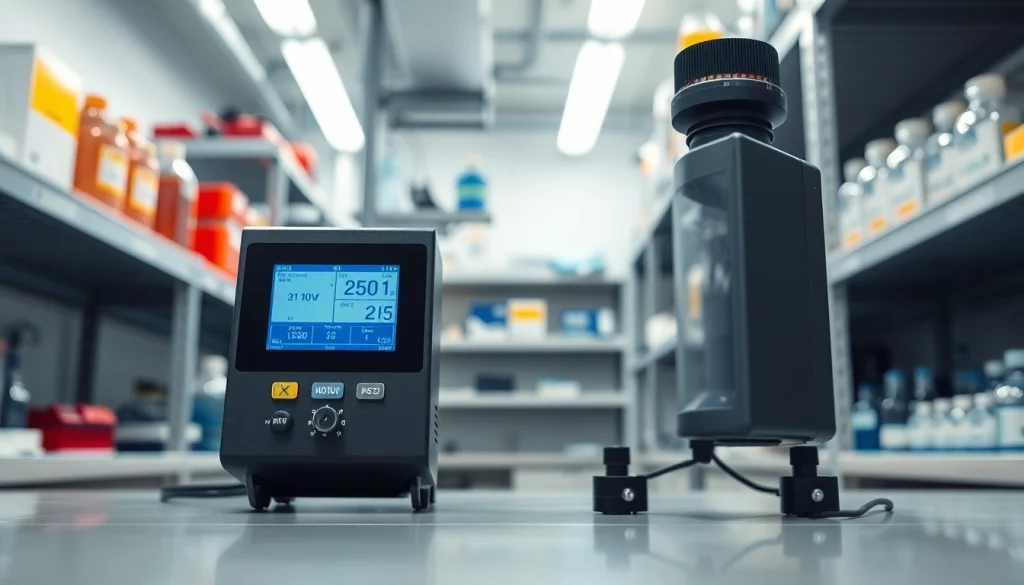
Understanding Hydrogen Cyanide and Its Risks
What is Hydrogen Cyanide?
Hydrogen cyanide (HCN) is a colorless, highly toxic chemical compound with a faint bitter almond odor. It is a simple molecule consisting of one carbon atom, one nitrogen atom, and one hydrogen atom. This compound is known for its potential to be both an industrial chemical and a chemical weapon. Historically, hydrogen cyanide has been used in various applications, primarily in the production of plastics, dyes, and pesticides. Its volatility and high toxicity classify it as a serious hazard in many industrial environments, making hydrogen cyanide detection crucial for maintaining safety standards.
The Dangers of Hydrogen Cyanide Exposure
Exposure to hydrogen cyanide can have severe effects on human health, primarily targeting the respiratory and cardiovascular systems. Inhalation of even low concentrations can lead to symptoms such as headache, dizziness, confusion, and in severe cases, unconsciousness or death. The mechanism of toxicity is attributed to the compound’s ability to inhibit cellular respiration, preventing cells from utilizing oxygen effectively.
Moreover, longer-term or chronic exposure can result in a range of neurological issues, as well as potential reproductive and developmental effects. Workers in industries such as chemical manufacturing, metal processing, and agricultural production are particularly at risk, underscoring the need for effective Hydrogen Cyanide monitors to mitigate these dangers.
Common Industries at Risk
Numerous industries utilize hydrogen cyanide or are at risk for exposure due to its presence in the environment. Key sectors include:
- Chemical Manufacturing: HCN is used in the production of synthetic fibers, plastics, and agricultural chemicals.
- Metallurgy: Hydrogen cyanide can be released during metal processing, particularly in the extraction of precious metals.
- Electronics: Its use in producing semiconductors means workers in this sector face potential exposure.
- Fumigation: HCN is employed as a fumigant for agricultural applications, posing risks to workers in the field.
Importance of Hydrogen Cyanide Monitors
Why Monitoring Hydrogen Cyanide is Critical
The primary purpose of hydrogen cyanide monitoring is to safeguard the health and safety of workers in high-risk environments. Early detection of HCN is crucial because it allows for immediate evacuation and emergency response, minimizing exposure to toxic levels. Monitoring not only protects workers but also helps organizations comply with regulations set forth by occupational safety and health administrations.
Furthermore, monitoring systems can integrate with other safety protocols in an organization’s risk management strategy, enhancing overall workplace safety. Implementing hydrogen cyanide monitors reduces the risk of accidents, ultimately resulting in lower insurance costs and fewer liabilities.
Types of Hydrogen Cyanide Monitors Available
Hydrogen cyanide monitors come in various formats, each designed to meet specific needs. The main types include:
- Portable Monitors: These handheld devices are essential for workers who need to move around frequently in environments where HCN is present. They provide real-time data on hydrogen cyanide levels.
- Fixed Monitors: These are installed in specific locations, providing continuous monitoring in high-risk areas, such as chemical processing plants or laboratories.
- Wireless Monitors: These systems incorporate advanced technologies like Bluetooth and Wi-Fi, allowing for remote data collection and alerts. They are suitable for larger facilities where monitoring across multiple areas is necessary.
- Multi-Gas Detectors: Some monitors can detect multiple gases, including hydrogen cyanide, making them versatile choices for comprehensive air quality control.
Choosing the Right Monitor for Your Needs
Selecting the right hydrogen cyanide monitor involves evaluating several factors:
- Environment: Consider whether you need a portable or fixed system based on your operational needs.
- Sensitivity: Different monitors have varying sensitivity levels—choose one that can detect HCN concentrations relevant to your work environment.
- Response Time: Quick response time is crucial for safety. Look for monitors that provide immediate alerts at dangerous concentration levels.
- Calibration Frequency: Some devices require more frequent calibration than others, impacting your maintenance schedule.
Best Practices for Using Hydrogen Cyanide Monitors
Installation and Calibration Techniques
Proper installation and calibration of hydrogen cyanide monitors are critical to their effectiveness. Installation should be done according to manufacturer guidelines, ensuring monitors are placed in areas where hydrogen cyanide is likely to accumulate. Regular calibration is essential; most monitors need calibration at least annually or after significant exposure events. Calibration helps confirm that the monitor readings are accurate and timely, reflecting real-time HCN levels in the environment.
Regular Maintenance for Optimal Performance
To ensure hydrogen cyanide monitors operate at peak performance, regular maintenance checks should be implemented. This includes:
- Cleaning the sensors as per manufacturer instructions to prevent dust or debris from interfering with readings.
- Checking battery levels and replacing them periodically to ensure continuous operation.
- Testing the alarms to ensure they function correctly, providing timely alerts in case of dangerous HCN levels.
Employee Training and Safety Protocols
Investing in employee training is vital for effective hydrogen cyanide monitoring. Staff should be trained on:
- How to operate hydrogen cyanide monitors and interpret their readings.
- Recognizing symptoms of hydrogen cyanide exposure and emergency protocols for evacuation and treatment.
- Routine inspection and maintenance schedules to foster responsibility in keeping monitoring devices fully functional.
Monitoring Technology and Innovations
Advancements in Sensor Technology
Sensor technology is evolving rapidly, presenting opportunities for more reliable and precise hydrogen cyanide detection. Recent advancements include the development of:
- Electrochemical Sensors: These provide high sensitivity and selectivity for hydrogen cyanide, reducing false alarms from other gases.
- Photoionization Detectors (PIDs): PIDs can detect very low concentrations of hydrogen cyanide, expanding the range of monitoring capabilities.
- Optical Sensors: This technology uses infrared light to detect HCN concentrations, providing non-contact measurement.
Integrating Hydrogen Cyanide Monitors with Smart Systems
Integration of hydrogen cyanide monitors with smart safety systems enhances their functionality. Organizations are adopting IoT (Internet of Things) solutions to create networks of sensors that communicate to alert personnel rapidly of any dangerous levels.
Remote notifications allow for immediate action, while comprehensive data analytics help companies assess long-term trends and identify potential hazards. Smart systems can also sync with the organization’s overall safety software, facilitating smoother operational compliance and risk management processes.
Future Trends in Hydrogen Cyanide Detection
The future of hydrogen cyanide detection is promising with emerging trends aimed at improving safety. Efforts to develop:
- AI and Machine Learning: These technologies can process large amounts of monitoring data, identifying patterns that might indicate dangerous environmental changes before they become critical.
- Portable Technologies: Innovations are leaning towards devices with longer battery lives and smaller form factors, allowing workers to monitor their surroundings continuously without hindrance.
- Wearable Safety Technology: Developers are exploring wearable devices that can monitor ambient hydrogen cyanide levels through skin temperature changes or other physiological metrics.
Case Studies and Real-World Applications
Successful Implementations in Various Industries
Numerous industries have successfully implemented hydrogen cyanide monitors, showcasing their effectiveness in real-world applications. For example:
- Chemical Manufacturing Plant: A facility monitoring hydrogen cyanide concentrations rigorously reported a significant decrease in exposure incidents following the installation of real-time fixed monitors.
- Mining Operations: Mining companies equipped their workers with portable HCN monitors, decreasing emergency response times and surviving exposure crises.
Lessons Learned from Monitoring Incidents
Reviewing past incidents highlights the importance of hydrogen cyanide monitoring. In one unfortunate case, a chemical plant experienced a leak due to equipment failure, resulting in several injuries. The aftermath revealed shortcomings in their monitoring systems, prompting them to invest in advanced hydrogen cyanide detectors that minimize false readings and react promptly to dangerous levels.
Feedback from Users on Monitor Effectiveness
User feedback provides invaluable insights into the effectiveness of hydrogen cyanide monitors. Many employees report increased confidence in their safety procedures once reliable monitoring systems were installed. Consistently accurate notifications and user-friendly interfaces have led to praise for various monitor brands, impacting future purchasing decisions.