Choosing the Right AC DC TIG Welder: A Comprehensive Guide for Welders
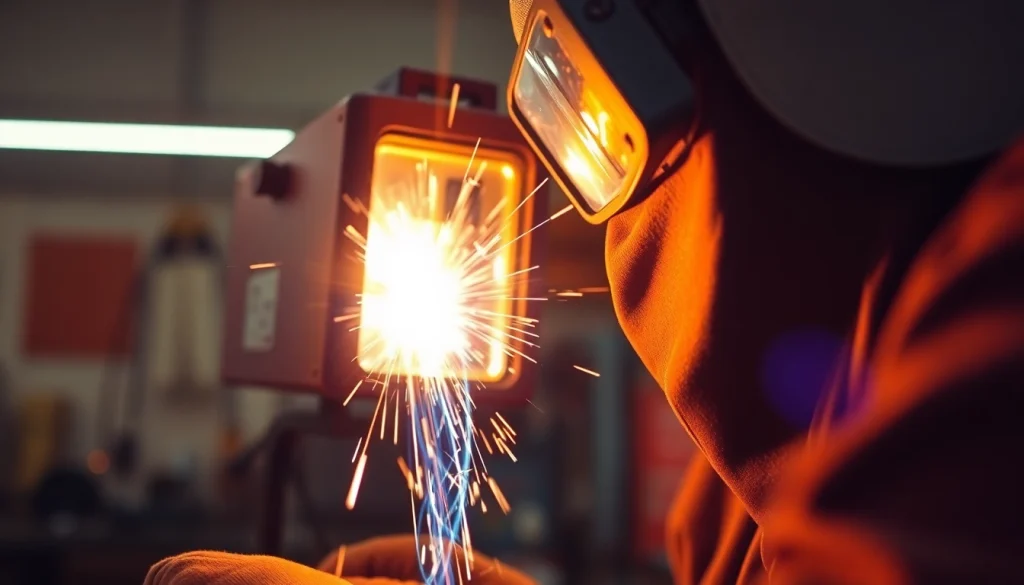
Understanding AC DC TIG Welders
What is an AC DC TIG Welder?
An AC DC TIG welder is a versatile welding machine capable of operating on both alternating current (AC) and direct current (DC). The ability to switch between AC and DC modes provides incredible flexibility for the welder, allowing them to tackle a wide range of materials and thicknesses with ease. This dual functionality is particularly beneficial for professionals who work with various metals like aluminum, stainless steel, and mild steel. In contrast to traditional welding methods, AC DC TIG welders use a non-consumable tungsten electrode to produce a clean and precise arc, resulting in superior weld appearances.
Applications of AC DC TIG Welding
AC DC TIG welders are commonly employed in industries including automotive, aerospace, and manufacturing, where precision and quality are paramount. They are particularly well-suited for:
- Aluminum Welding: The AC mode is ideal for welding aluminum due to the need for a cleaning cycle that removes oxides and impurities from the surface.
- Stainless Steel Fabrication: DC welding provides smooth and stable arcs, making it suitable for stainless steel applications.
- Pipe Welding: The precision provided by TIG welding is invaluable in pipe and tube applications, ensuring strong and defect-free joints.
Key Features to Look for in an AC DC TIG Welder
When selecting an AC DC TIG welder, it’s essential to consider features that can enhance your welding experience:
- Wattage and Amperage: Higher amperage allows for thicker materials to be welded effectively. Make sure to select a machine that fits the thickness of the materials you will work with.
- Input Power: Check whether the welder operates on single-phase or three-phase power supply, affecting its portability and application in various environments.
- Control Options: Look for machines with advanced controls for adjusting heat settings and travel speed, as well as features like pulse welding and waveforms customization.
- Cooling Mechanism: An effective cooling system extends the life of your equipment and is crucial for prolonged welding tasks.
The Benefits of Using AC DC TIG Welders
Versatility: Handling Different Materials
The versatility of an AC DC TIG welder allows it to handle a diverse range of materials including aluminum, stainless steel, copper, and more. This adaptability makes it a favored choice for both professional welders and hobbyists. The choice between AC and DC modes permits adjustments based on specific metal characteristics—AC is necessary for aluminum while DC excels with thicker materials like stainless steel and mild steel. This feature is valuable for workshops that handle various fabrication projects.
Precision in Welding Techniques
One of the significant advantages of TIG welding is the precision it offers. The process enables the welder to focus extremely fine heat onto the workpiece, minimizing the risk of warping or distortion. This precision is particularly crucial in applications demanding high standards, such as in aerospace components or intricate art pieces. Being able to fine-tune arc length and travel speed results in quality welds that can be visually inspected and structurally sound.
Efficiency in Performance and Cost
While the initial investment in acquiring an AC DC TIG welder can be substantial, the overall efficiency contributes to lower long-term costs. TIG welding minimizes waste and often requires fewer filler materials, thereby reducing operational expenses. Moreover, higher-quality welds decrease the likelihood of repairs or reworks, saving both time and resources. With improved efficiency, businesses can take on more projects, leading to greater profitability.
Selecting the Best AC DC TIG Welder for Your Needs
Identifying Your Welding Projects
Before purchasing an AC DC TIG welder, it’s important to define the types of projects you will be tackling. Consider the thickness and composition of the materials, the frequency of use, and the specific welding environment. For instance, a fabricator working on aluminum chassis for race cars would need a welder with strong AC capabilities and higher amperage settings, while repair work on stainless steel appliances may require a unit focused on DC capabilities.
Comparing Top Brands and Models
Several reputable brands are known for manufacturing high-quality AC DC TIG welders, including Everlast, Miller, Lincoln Electric, and PrimeWeld. When comparing models, assess user reviews, warranty options, and after-sales support. Consider also the additional features each brand offers, such as digital displays, built-in safety mechanisms, and upgraded cooling systems. It’s advisable to watch demonstrations whenever possible and research specific models to ensure they align with your needs.
Price Range and Budget Considerations
The price of AC DC TIG welders can vary significantly based on features and brand reputation. Entry-level models can start around $300, while high-end machines might exceed $5,000. Establishing a clear budget is crucial, but equally important is valuing the features and capabilities the machine offers. It is often worthwhile to invest a little more for extended warranties or advanced features that can improve the machine’s longevity and performance. Additionally, consider the availability of consumable parts and their costs in your overall expense planning.
Common Challenges with AC DC TIG Welding
Understanding Common Issues and Solutions
Even skilled welders may experience challenges while using AC DC TIG welders. Common issues include:
- Inconsistent Arc Stability: This can be caused by incorrect settings or improper technique. Ensure the machine is set correctly for the material type, and practice maintaining a steady hand.
- Weld Contamination: Proper surface preparation is vital. Ensure that the material surface is clean and free from oils or contaminants before beginning to weld.
- Overheating Electrodes: Monitor the duty cycle of the welder and ensure it is not being used beyond its rated capacity to prevent overheating and damage.
Maintaining Your AC DC TIG Welder
Regular maintenance is vital to ensure the longevity and peak performance of your AC DC TIG welder. Key practices include:
- Routine Cleaning: Keep the welder and its components clean from dust and debris. Pay special attention to the torch, including the tungsten electrode and nozzle.
- Inspect Connections: Regularly check all electrical connections for signs of wear or corrosion. Tighten any loose connections to maintain electrical integrity.
- Coolant Replacement: If your welder uses a coolant system, ensure that the coolant is replaced regularly to prevent overheating.
Safety Tips for TIG Welding
Safety is paramount when operating an AC DC TIG welder. Follow these recommendations to maintain a secure working environment:
- Protective Gear: Always wear proper protective gear including gloves, a welding helmet with a suitable lens shade, and protective clothing.
- Ventilation: Ensure your workspace is well-ventilated to avoid inhaling harmful fumes during the welding process.
- Electrical Safety: Understand the electrical requirements of your welder and ensure it is properly grounded to avoid shock hazards.
Conclusion: Mastering AC DC TIG Welding Techniques
Advanced Techniques for Experienced Welders
Once proficient with standard techniques, experienced welders can explore advanced methods such as:
- Pulsed TIG Welding: This technique involves varying the current levels, which helps to prevent heat buildup and allows for better control.
- Using Weave Patterns: Varying your movement creates different heat input and improves the quality of the weld.
- Multi-Pass Welding: In materials that are too thick for a single pass, a multi-pass technique can achieve the necessary penetration and strength.
Continuing Education and Resources
Continuous improvement in welding skills can be achieved through various resources such as:
- Workshops and Seminars: Engage in hands-on workshops to learn from experienced professionals and acquire new skills.
- Online Courses: Many platforms offer courses related to advanced techniques, safety practices, and maintenance.
- Community Forums: Joining welding communities allows you to share experiences and learn from fellow welders.
Connecting with the Welding Community
Building relationships within the welding community can provide support and motivation. Joining local welding clubs or participating in online forums enables members to exchange ideas, share challenges, and present projects that inspire others. Resources like ac dc tig welder discussions can offer insights and recommendations that enhance one’s knowledge and experience in welding.