Essential Insights on Nitrogen Regulators: Safety, Selection, and Applications
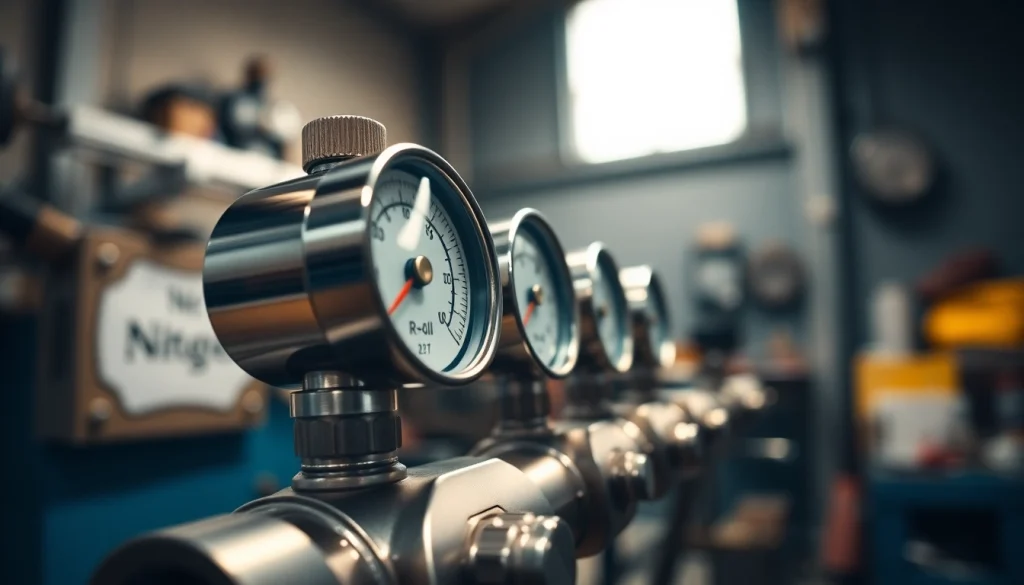
Understanding Nitrogen Regulators
Nitrogen regulators are essential tools used across various industries to control the pressure and flow rate of nitrogen gas. As an inert gas commonly used in applications ranging from food packaging to HVAC systems, ensuring that nitrogen is delivered efficiently and safely is paramount. In this article, we will explore the fundamental aspects of nitrogen regulators, including their purpose, components, applications, and much more. For those looking to purchase a nitrogen regulator, a wide variety of options are available, including those found at nitrogen regulator suppliers.
What is a Nitrogen Regulator?
A nitrogen regulator is a mechanical device that controls the pressure of nitrogen gas as it is released from a storage cylinder or tank to a specific application. These regulators ensure that the gas is delivered at a consistent and manageable pressure, preventing fluctuations that can lead to inefficiencies or hazardous conditions. They are designed to reduce the high pressure of nitrogen gas stored in cylinders to a lower, usable pressure for various applications.
Key Components and Their Functions
Nitrogen regulators consist of several key components that work together to regulate the gas flow. Understanding these components is essential for effective usage and maintenance:
- Body: The main structure of the regulator, which houses internal components and connects to the nitrogen gas source.
- Inlet Fitting: The connection point for the nitrogen cylinder or supply line, typically using a CGA fitting for secure attachment.
- Diaphragm: A crucial part that responds to pressure changes, maintaining the desired output pressure by adjusting the gas flow.
- Adjustment Screw: A user-adjustable mechanism that alters the output pressure by regulating the diaphragm position.
- Outlet Fitting: The fitting that connects to downstream equipment or tools, allowing the regulated nitrogen to flow into the application.
Common Applications of Nitrogen Regulators
Nitrogen regulators have a wide range of applications across various industries. They are crucial in maintaining the integrity and functionality of processes reliant on nitrogen gas:
- Food and Beverage: Used in the packaging of food products to displace oxygen and prolong shelf life.
- HVAC Systems: Essential for pressure testing HVAC systems and ensuring efficient operation within refrigeration cycles.
- Welding: Utilized in MIG and TIG welding processes where nitrogen is used to protect molten metal from oxidation.
- Laboratories: Employed in various experimental procedures where controlled environments are necessary.
- Electronics Manufacturing: Involved in manufacturing processes that require inert gas environments to prevent contamination.
Choosing the Right Nitrogen Regulator
Choosing the right nitrogen regulator can significantly impact the efficiency and safety of your nitrogen applications. Several factors should be considered in this decision-making process.
Factors to Consider When Selecting a Nitrogen Regulator
When selecting a nitrogen regulator, consider these key factors:
- Pressure Requirements: Determine the output pressure needed for your application; some applications may need only low pressure, while others may require high-pressure systems.
- Flow Rate: Assess the required flow rate in standard cubic feet per minute (SCFM) to ensure the regulator can meet demands without pressure drop.
- Material Compatibility: Ensure that the materials of the regulator are suitable for the gases and environments it will be used in, to prevent corrosion or degradation.
- Adjustment Mechanism: Evaluate whether you need a fixed or adjustable pressure regulator based on your application’s flexibility requirements.
- Size and Connection Type: Ensure that the regulator fits your existing equipment and that the inlet and outlet connections are compatible.
Pressure Ratings and Specifications
Understanding the pressure ratings of nitrogen regulators is crucial in selecting the appropriate one. Regulators come with various configurations that can handle different inlet pressures, typically ranging from 2000 to 3000 psi, and can regulate the output to anywhere from 0 to 150 psi or more, depending on the specific requirements of the application. Make sure to refer to the manufacturer’s specifications and choose a regulator that meets the demands of your project.
Popular Brands and Models of Nitrogen Regulators
Several reputable brands manufacture nitrogen regulators, each offering different models with unique features. Some popular names include:
- Victor: Known for their durable and reliable welding equipment, Victor offers nitrogen regulators designed especially for welding applications.
- Smith: They provide a wide range of regulators suitable for various applications, with a reputation for precision and quality.
- Uniweld: Their nitrogen regulators are popular for offering reliable performance in HVAC applications.
Installation and Safety Precautions
Proper installation and adherence to safety precautions are vital to the effective functioning of nitrogen regulators.
Step-by-Step Installation Guide for Nitrogen Regulators
Follow these steps to ensure safe and effective installation of a nitrogen regulator:
- Gather Necessary Tools: Ensure you have all tools needed for installation, including wrenches and sealants.
- Check Equipment: Inspect the nitrogen cylinder and regulator for any signs of damage or wear.
- Attach the Regulator: Securely connect the regulator to the nitrogen cylinder using the appropriate fitting.
- Adjust the Output Pressure: Turn the adjustment screw to set the desired output pressure before opening the nitrogen supply.
- Test for Leaks: Use a soap solution or leak detection fluid to check all connection points for leaks before operational use.
- Begin Operation: Slowly open the cylinder valve to allow nitrogen to flow to the regulator and check readings on the pressure gauge.
Safety Standards to Follow When Using Nitrogen Regulators
Safety is paramount when working with pressurized gases. Follow these safety standards:
- Use Personal Protective Equipment (PPE): Always wear appropriate PPE, including gloves and goggles, when handling nitrogen regulators.
- Ventilation: Ensure workspaces are well-ventilated to prevent the buildup of nitrogen, which can displace oxygen in enclosed spaces.
- Secure Tools and Equipment: Ensure that all equipment is mounted securely and tools are stored away when not in use to prevent accidents.
Common Mistakes to Avoid During Installation
Avoid the following common mistakes during installation:
- Neglecting to Check for Leaks: Always conduct thorough leak checks to prevent potential hazards.
- Incorrect Pressure Settings: Ensure that the output pressure is set according to the application’s specifications to avoid equipment damage.
- Improper Connections: Use the appropriate fittings and ensure that connections are secure to prevent accidental disconnections during operation.
Maintenance of Nitrogen Regulators
Regular maintenance is essential to prolong the lifespan and ensure the safety of your nitrogen regulators.
Routine Maintenance Checks for Longevity
Implement a routine maintenance schedule that includes the following checks:
- Inspect Connections: Regularly inspect all fittings and connections for signs of wear or damage.
- Check Pressure Gauges: Ensure that pressure gauges are functioning correctly and replace them if they show signs of malfunction.
- Clean Regulators: Regularly clean the body and components of the regulator to prevent dust and debris buildup.
Identifying Signs of Wear and Tear
As with any piece of equipment, it’s essential to recognize when your nitrogen regulator shows signs of wear:
- Leaking Gas: If you notice nitrogen leaking from any points, it’s a sign of valve or fitting failure.
- Inconsistent Pressure Readings: Fluctuating pressure readings can indicate a malfunctioning diaphragm or other internal components.
- Physical Damage: Visible cracks, dents, or corrosion on the regulator’s body indicate it may need repair or replacement.
Best Practices for Cleaning Nitrogen Regulators
To effectively clean nitrogen regulators:
- Follow Manufacturer Guidelines: Always refer to specific cleaning recommendations provided by the manufacturer.
- Use Appropriate Cleaning Agents: Avoid harsh chemicals that can deteriorate materials; instead, use gentle cleaners suitable for metal surfaces.
- Reassemble Carefully: After cleaning, ensure that all components are reassembled correctly to maintain functionality.
Troubleshooting Common Issues with Nitrogen Regulators
Even with proper installation and maintenance, issues can arise. Knowing how to troubleshoot them can save time and money.
Identifying Pressure Regulation Problems
Common indicators of pressure regulation problems include:
- Unexpected High or Low Pressure: This can often be traced back to a blocked diaphragm or issues with the adjustment screw.
- No Gas Flow: A lack of gas flow could indicate a malfunctioning valve or a completely depleted nitrogen cylinder.
- Pressure Fluctuations: Variability in output pressure signals possible diaphragm failure or an improper seal.
Solutions for Leaks and Malfunctions
Upon identifying issues, here are some corrective actions to take:
- Replace Damaged Seals: If leaks are detected, check and replace seals thoroughly.
- Adjust the Diaphragm: Reassess and adjust the diaphragm to ensure optimal operation.
- Consult Documentation: Manufacturer documentation often contains specific malfunctions explanations and solutions.
When to Seek Professional Help
If troubleshooting does not yield solutions, consider seeking professional assistance, particularly in the following situations:
- Persistent Leaks: If leaks persist despite attempts to fix them.
- Severe Physical Damage: Any indications of severe damage that could pose safety risks.
- Complex Pneumatic Systems: If you are using nitrogen in complex pneumatic systems that require specialized knowledge.