How to Choose the Right AC DC TIG Welder for Your Welding Projects
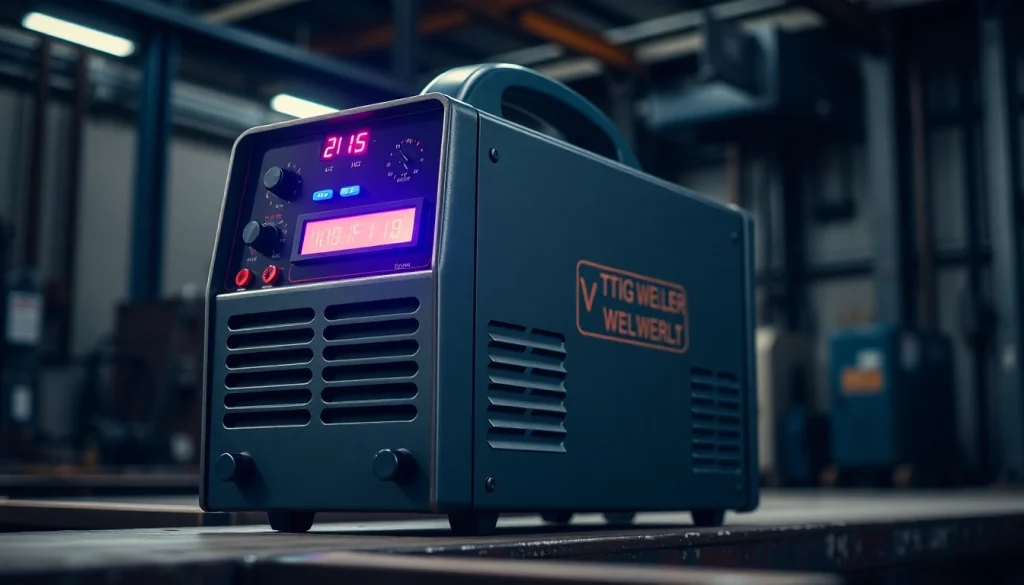
Understanding AC DC TIG Welders
What is an AC DC TIG Welder?
An AC DC TIG welder is a versatile welding machine that caters to a diverse array of materials and applications by allowing users to toggle between alternating current (AC) and direct current (DC). The primary advantage of this switching capability is the increased flexibility it provides. While AC is typically preferred for aluminum and magnesium welding, DC is ideal for ferrous metals like steel and stainless steel. By utilizing an ac dc tig welder, welders can achieve high-quality welds across different materials, making it an essential tool for professionals and hobbyists alike. These welders are equipped with sophisticated features, including adjustable amperage and precise control settings, allowing for methodical manipulation of heat and speed during operations.
The Advantages of AC vs. DC Welding
The choice between AC and DC welding has significant ramifications on the quality of welds and the ease with which they are achieved. Here’s a closer look at the advantages of each:
- Alternating Current (AC): AC welding is particularly effective for non-ferrous materials, primarily aluminum, due to its ability to clean the weld area through a process known as arc cleaning. The positive cycle of AC helps to remove oxides and contaminants, ensuring better fusion and weld integrity. Additionally, AC welders can weld at higher frequencies, which can enhance the quality and aesthetics of the weld.
- Direct Current (DC): DC welding is often regarded for its stability and consistency, producing a smoother arc and enhanced heat retention. This makes DC well-suited for welding ferrous materials, allowing for stronger and deeper weld penetration. With DC, users can also reverse the polarity to shift between welding and cutting, further enhancing the machine’s versatility.
Key Applications for AC DC TIG Welding
AC DC TIG welders are used across various industries, each having distinct needs for precision welding. Some primary applications include:
- Aerospace: High standards for material joining in aerospace necessitate the precision and control provided by TIG welding, especially for complex components.
- Automotive: The automotive industry relies on TIG welds for frame repairs and custom fabrication, often requiring seamless joins that can withstand stress.
- Shipbuilding: The ability to weld aluminum and steel makes AC DC TIG welders indispensable in shipbuilding, where both materials are frequently used.
- Artistic Projects: Fabricators and artists opt for TIG welding due to the aesthetics of the welds and the fine detail it permits in artistic metalwork.
Factors to Consider When Buying an AC DC TIG Welder
Power Output and Duty Cycle
When selecting an AC DC TIG welder, the power output and duty cycle are crucial factors. Power output, typically measured in amps, dictates the thickness of material you can effectively weld. A common range for portable welders is between 200 to 300 amps.
The duty cycle is the percentage of time the welder can operate without overheating. For instance, a machine rated at a 60% duty cycle at 200 amps means it can weld continuously for six minutes out of ten. Evaluating power requirements based on the types of projects you plan to undertake is essential for ensuring that your equipment can handle your workload.
Portability and User Features
Portability often plays a significant role in purchasing decisions, especially for professionals who move from job site to job site. Many modern AC DC TIG welders are designed with lightweight materials and built-in handles, making transport considerably easier.
User features also enhance usability. Look for adjustable controls for current and voltage, display panels for easier monitoring of settings, and additional features like a foot pedal for better control during welding operations. Some models come with built-in safety features, including thermal overload protection and gas flow charts, which can prove invaluable for both beginners and seasoned welders.
Brand Reputation and Warranty Considerations
Researching brand reputation is equally important, as established brands often provide more reliable products and better customer service. Seek out manufacturers known for their high-quality AC DC TIG welders, backed by comprehensive warranties that cover parts and labor. A robust warranty can be a signal of the manufacturer’s confidence in their product, as well as an added layer of security for your investment.
Top AC DC TIG Welders in the Market
Comparative Analysis of Leading Brands
This section explores some of the leading brands in the AC DC TIG welder market, analyzing their strengths:
- Everlast: Known for their balance of affordability and features, Everlast offers models like the PowerTIG 200DV that provide both AC and DC capabilities with a high duty cycle.
- Miller: Renowned for their durable and powerful welders, Miller’s Syncrowave line is often favored in industrial applications due to their reliability and performance.
- Lincoln Electric: A trusted name in welding equipment, Lincoln’s Aspect series offers impressive functionalities, catering particularly to the aerospace and automotive sectors.
- PrimeWeld: Known for budget-friendly options, PrimeWeld’s TIG 225X combines quality performance with an accessible price point, ideal for beginners and hobbyists.
Best Budget Options for Beginners
For those new to TIG welding, several budget-friendly options provide excellent starting points without compromising on performance:
- Eastwood TIG 200: This affordable option is equipped with features that cater to entry-level welders, providing great quality for the price.
- YesWelder TIG-205DS: Known for its portability and lightweight design, this welder offers dual voltage compatibility and is ideal for those starting out.
- Hobart Handler 140: While primarily marketed as a MIG welder, it provides versatility through plasma cutting capabilities, making it a solid investment for a multi-purpose unit.
High-End Models for Professionals
Professionals seeking advanced functionality may consider high-end models, which typically include features designed to meet rigorous industry standards:
- Miller Syncrowave 300: This high-performing TIG welder is suitable for heavy-duty applications and offers advanced features such as wireless foot control and exceptional arc stability.
- Lincoln Electric Aspect 375: This model is engineered for precision with unmatched control, making it suitable for critical applications in aerospace and motorsports.
- Everlast 201 DV: Combines digital controls with inverter technology for smooth arc and various welding capabilities, ideal for experienced welders.
Tips for Getting the Most Out of Your AC DC TIG Welder
Maintenance Best Practices
Regular maintenance is essential for keeping your AC DC TIG welder in optimal condition. Here are several tips:
- Keep the machine clean and free of debris. Dust and spatter can impede airflow, causing overheating.
- Regularly inspect and clean the welding torch, ensuring the electrodes are in good condition and replaced when necessary.
- Check gas connections for leaks, and ensure the gas flow rates are optimal for your welding requirements.
- Periodically review the internal components for signs of wear or damage to prevent major malfunctions.
Common Welding Techniques with TIG
To achieve high-quality welds, understanding and mastering various TIG welding techniques is crucial:
- Stringer Bead Technique: This technique is ideal for welding thin material. It focuses on making a narrow, stacked bead of weld metal that offers high precision.
- Weaving Technique: A weaving motion can be effective for thicker materials, allowing for broader beads and increased heat input.
- Push vs. Pull Technique: Welding direction can affect the quality of the bead. Using a push technique can provide a more fluid weld, while the pull technique can help in controlling heat better.
Safety Tips When Operating TIG Welders
Ensuring safety while operating TIG welders is paramount. Here are key safety practices to follow:
- Personal Protective Equipment (PPE): Always wear appropriate PPE, such as welding gloves, helmets with dark lenses, and flame-resistant clothing to protect against sparks and UV radiation.
- Ventilation: Ensure that your workspace is well-ventilated to prevent inhalation of harmful fumes.
- Keep Fire Extinguishers Accessible: Always have fire extinguishers within reach in case of emergencies.
- Proper Use of Argon Gas: If using argon gas for shielding, ensure all connections are secure to prevent leaks.
Troubleshooting Common Issues with AC DC TIG Welders
Identifying Arc Stability Problems
Arc stability issues can lead to poor weld quality. Identifying these problems often requires analysis of several factors:
- Electrode Quality: Ensure that the tungsten electrode is properly ground and clean. Contaminants can disrupt the arc.
- Gas Flow Rate: An inadequate gas flow can cause the shield to falter and lead to oxidation, impacting the weld.
- Current Settings: Adjust the current settings according to the thickness of the material being welded. Too much current can create an unstable arc.
Fixing Inconsistent Welding Quality
Inconsistent welding quality can stem from several sources. Here’s how to troubleshoot the issue:
- Review the fit-up of the pieces being welded and ensure they are aligned correctly.
- Check settings on the welder and ensure they match the material specifications.
- Inspect the filler material for compatibility with the base metal.
When to Seek Professional Assistance
If faced with persistent issues that are beyond your troubleshooting skills or if your welder requires extensive repairs, it may be best to seek professional assistance. Signs that you should consult an expert include:
- Frequent electrical issues or intermittent malfunctions of the welder.
- Persistent overheating problems that worsen despite maintenance.
- Visible damage to internal components of the welder, indicating the need for specialized repairs.